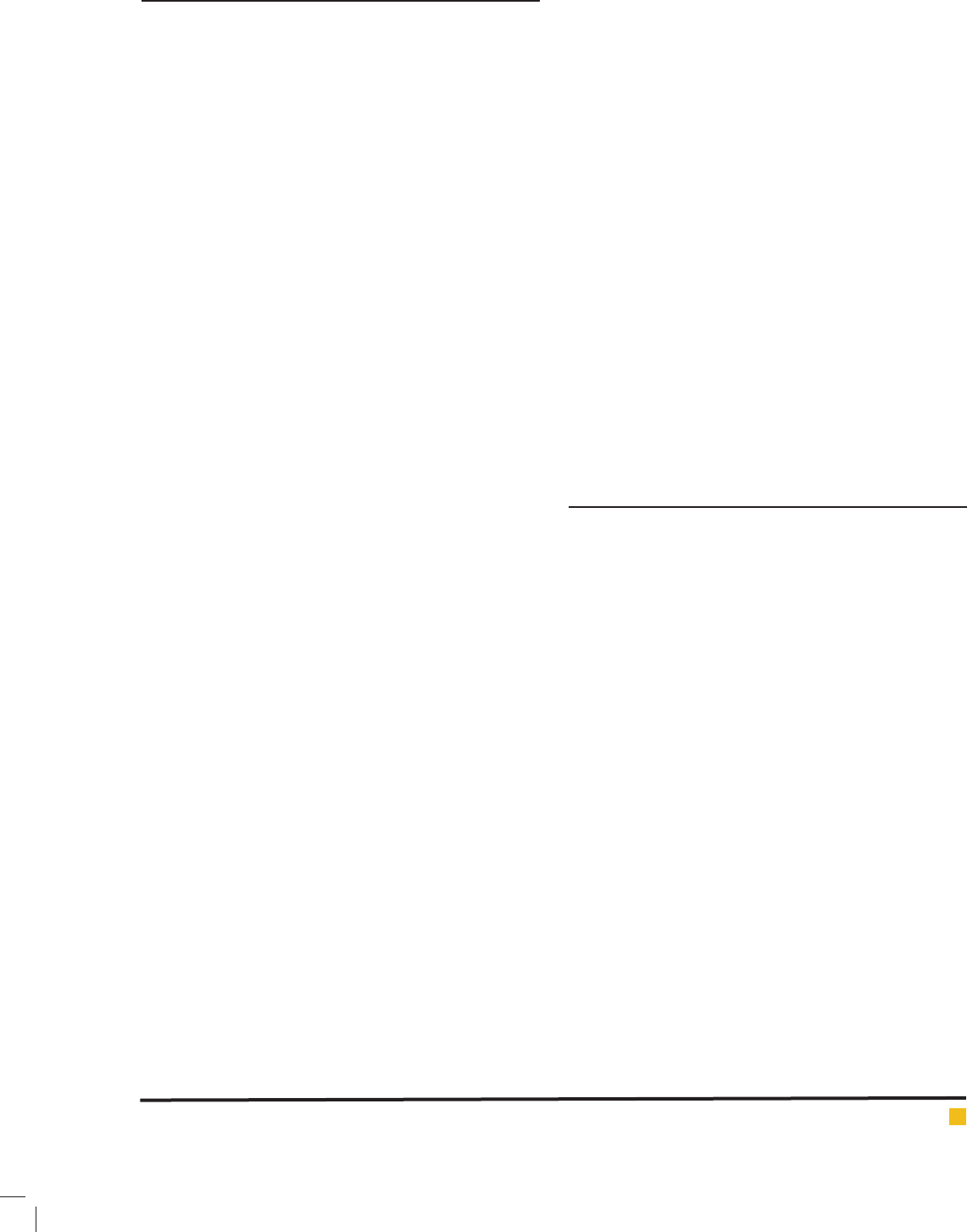
Ebdam et al.
INTRODUCTION
The research and developments on new engineering
materials belong to the important elds of material sci-
ence. One can see the continuous competition between
the traditional inorganic engineering materials and pol-
ymers. Since polymeric materials (including composites)
are promising, due to their economic versatile applica-
bility, they are widely used in many applications, such
as housing materials, transport and electrical engineer-
ing (Almeras et al. 2003; Anna et al. 2002; Bourbigot
et al. 1996a; Bourbigot et al. 1996b). These commercial
polymers are easily ammable. The ame retardant can
act in various ways i.e. physically or chemically. Many
types of ame retardants are used in consumer prod-
ucts (Troitzsch, 1990; Sain, 2004; Zhu, 2003). They are
mainly phosphorus, antimony, chlorides and bromides,
magnesium and boron-containing compounds (Seymour
et al. 1978).
Al(OH)3can act also as a reinforcing agent and smoke
suppressant additive with low or zero emissions of toxic
or hazardous substances. The main advantages of poly-
meric materials over many metal compounds are high
toughness, corrosion resistance, low density and ther-
mal insulation. Improvement of the ame retardancy
and thermal stability of polymers is a major challenge
for extending their use for most applications. The higher
level of ame retardancy of nanoparticles is due to their
bigger surface to volume fractions which let them dis-
perse into the polymeric matrix homogeneously, and
hence leads to formation of a compact char during the
combustion (Grigsby et al. 2005; Wang et al. 2007; Kul-
janin et al. 2006).
Poly(methyl methacrylate) (PMMA) isa highly am-
mable polymer, improving its thermal stability is very
important. There are several re retardants available in
the market. Although they improve the re resistance of
PMMA, they have a lot of disadvantages. Many addi-
tives are effective only at high loadings, generally from
10 wt% to 40 wt%, which changes the physical proper-
ties of the polymer. Most ame retardants additivesare
halogenated compounds (Bundersek et al. 2012a). On
the other hand, metaloxides are halogen-free products,
which can also be used for improving thermal stabil-
ity and re properties of PMMA. Aluminum hydrox-
ide (Al(OH)3) and magnesium hydroxide (Mg(OH)2) are
environmentally benign, butneed to be added in high
concentrations to be effective (Beyer, 2002). Trans-
parency of PMMA in the visible region is reason that
PMMA is an importantthermoplastic for numerous uses
(Beyer, 2005; Beyer, 2002; Chiang et al. 2009; Bundersek
et al. 2012b).
Inorganic compound magnesium hydroxide [Mg(OH)
2] as a smoking- and toxic-free additive has been exten-
sively used in halogen-free ame-retardant polymeric
materials. However, its fatal disadvantages are low
ame-retardant ef ciency and thus very large usage
amount, which lead the mechanical properties of a ame-
retardant polymeric material to drop down sharply. The
surface modi cation of magnesium hydroxide in order
to increase the compatibility between Mg(OH)2 particles
and polymers can enhance the mechanical strength of
composites (Wang et al. 2001).
Finally, to improve the properties of composites
made of PMMA, some changes in proposed structures
are necessary. Therefore, in this study, Nano-magnesium
hydroxide and aluminum hydroxide nanoparticles as
mineral retardant llers are synthesized and identi ed
by XRD and SEM. Then, composites of PMMA with dif-
ferent ratios of Mg (OH) 2 were built DSC-TGA and LOI
test were carried out on them. At the end, composites
composed of PMMA with different ratios of Mg(OH)2
and Al(OH)3 were made and the same tests with the
previous composites were done on them and thermal
behavior of composites containing aluminum hydrox-
ide and composites lacking aluminum hydroxide were
compared.
MATERIALS AND METHODS
All materials and solvents used in the synthesis of Nano
magnesium hydroxide and Nano aluminum hydroxide
were purchased from Sigma Aldrich and Merck and used
without any further puri cation. the melting points (ºC)
of the complexes were recorded on a Kruss instrument
and TG/DSC curves were obtained from a Diamond TGA
PerkinElmer 60 Hz. Poly methyl methacrylate (PMMA)
was obtained from I Tech polymer company Iran with
melt mass ow rate (MFR) of 0.9 – 27 g/10 min at 125ºC
and density 1.15 ‐ 1.19 g/cm3.. Infrared spectra were
recorded as KBr disks on Tensor 27 Bruker spectropho-
tometer. The evaluation of Al(OH)3oxide and synthe-
sized Nano composites were monitored by powder X-ray
diffraction Philips PW 1800 diffractometer with Cu K
radiation. Atomic force microscopy was carried out on
a Denmark Dual scope/Raster scope C26, DME micro-
scope. Scanning electron microscopy measurements was
performed on a VEGA\\TESCAN at an accelerating volt-
age of 15 kV. The LOI values were measured using a ZRY
type instrument (made in China) on the sheets of120 · 60
·3 mm3 according to ASTM D2863-77 standard.
2.1 Synthesis of Nano magnesium hydroxide
To prepare magnesium hydroxide nanoparticles, rst 5
g (MgSO4.7H2O) was solved in 40 ml of deionized water
and 5 ml of sodium hydroxide was added to it. Then, the
obtained solution was stirred with 1600 rpm for 1 hour
BIOSCIENCE BIOTECHNOLOGY RESEARCH COMMUNICATIONS ENHANCED FIRE RETARDANCY OF POLY METHYL METHACRYLATE 55