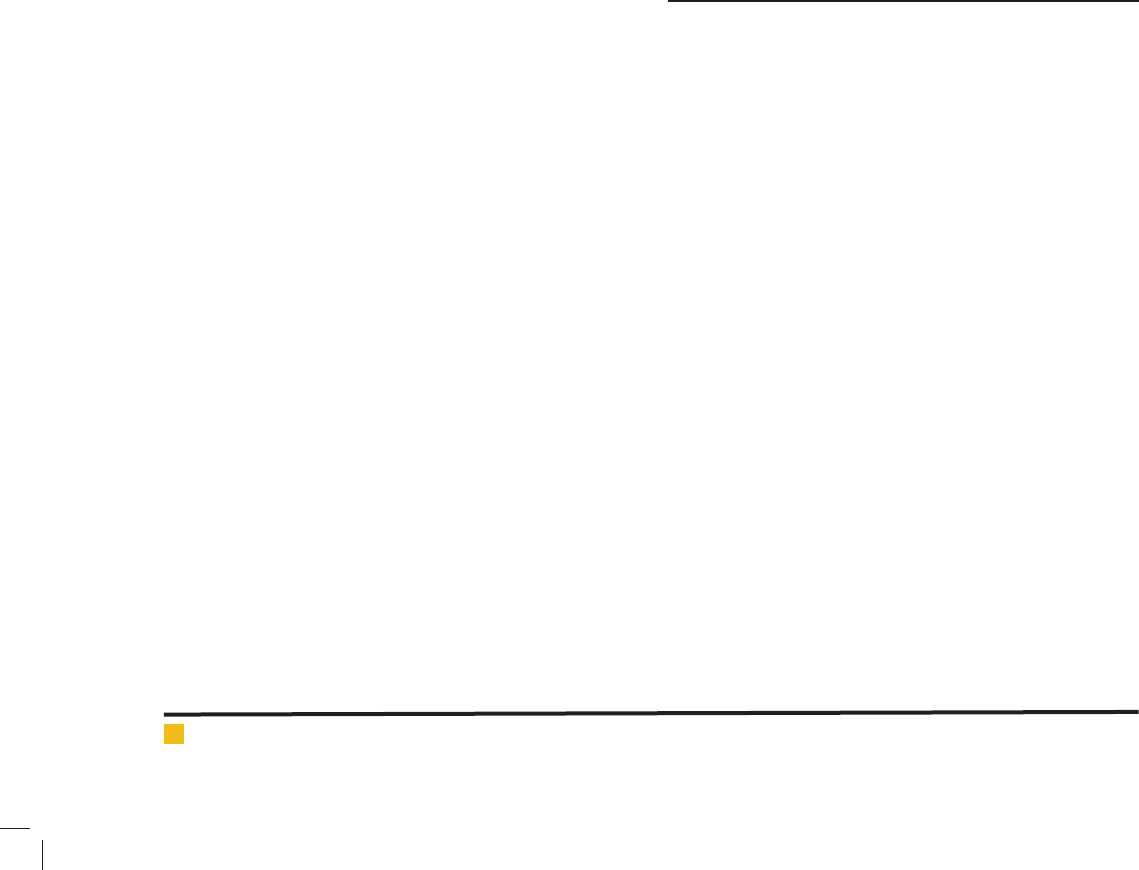
162 A CASE STUDY ON SIMULATION AND OPTIMIZATION OF ARTIFICIAL LIFT METHODS BIOSCIENCE BIOTECHNOLOGY RESEARCH COMMUNICATIONS
Azdarpour, Karaei and Dabiri
Bahadori et al. (2001) performed a simulation study
using PVD data along with uid and multiphase ow
correlations. They monitored the actual pressure and
temperature data to determine the point of gas injection
and construct the gas lift performance curve. They used
solution nodal method to determine the optimal gas lift
conditions including optimum injection depth, optimum
wellhead pressure, optimum production rate and mini-
mum injection gas volume. Their analysis showed that
the optimum production rate of 2200 bbl/day and opti-
mum injection gas volume of 1.1 MM SCF/day could
be gained using gas lift process. In addition, they also
concluded that the optimum gas liquid ratio is about
2100 SCF/bbl where increasing the gas liquid ratio from
its optimum value has no signi cant effect on produc-
tion rate.
de Souza et al. (2010) simulated the process of con-
tinuous gas lift using an optimization algorithm cou-
pled to a stationary two phase ow network model. They
declared that the solution of the optimization system
could be used for the injected gas ow rate to maxi-
mize the production rate and pro t as well as lowering
the capital cost of the process. Their study particularly
focused on two cases, an offshore single well case and
a complex subsea system. The analysis on offshore well
showed that the gas lift system could be optimized to
yield the maximum oil production for different well
pressure, while maximizing the pro t gained from the
process. At the second case study, a complex petroleum
production system with multiple wells is simulated and
optimized to obtain the optimal design considering
annualized costs of compressor, turbine driver, gas pipe-
lines and fuel gas consumption.
In another study by Mahmudi and Sadeghi (2013) the
gas lift system was optimized to maximize the pro t of
the well for a long period of time. They investigated the
effects of gas injection rate, tubing diameter and sepa-
rator pressure on overall performance of gas lift sys-
tem. They developed a mathematical model coupled
to a combination of Marquardt optimization method
and a genetic algorithm to simulate the gas lift system.
Their results showed that production lifetime should be
divided into a number of consecutive operation intervals
with different tubing diameter, lift gas injection rates
and separator pressures and an optimum value for tub-
ing diameter.
Naderi et al. (2014) investigated the feasibility of arti-
cial lift selection in the Khesht eld. The Khesht eld is
located in in south of Iran and was discovered in 1992.
Asmari reservoir, which is one the most important oil
reservoirs is located in this eld. The authors performed
a comprehensive study to select the most suitable arti -
cial lift method, which can be applied in this eld. They
investigated different production scenarios including
natural ow, electrical submersible pump, and gas lift.
They concluded that, initially natural ow should be
considered. However, by increasing the water cut gas lift
can be implemented and if the water cut is too high the
electrical submersible pump can be utilized.
Ebrahimi and Khamehchi (2016) have investigated
the feasibility and effectiveness of the natural gas lift
(NGL) using supportive vector machine (SVM). They
optimized the process using particle swarm optimiza-
tion (PSO) and genetic algorithm (GA). The optimum
SVM parameters were determined by the PSO algorithm.
Taguchi experiment design was used to determine opti-
mum GA and PSO parameters. The simulation results
showed that SVM could be used effectively to simulate
the gas lift process.
In this study, the feasibility of gas lift implementation
in one of the oil reservoirs in Iran was investigated. The
reservoir characteristics data including rock and uid
properties were used as input data to be used in PIPESIM
software. In addition, different parameters including
tubing size, injection depth and ow rates were varied
to determine the optimum production scenario.
MATERIALS AND METHODS
SIMULATION STUDY
In order to perform the optimization study, PIPESIM
software was used. This software is capable of deter-
ming optimum prodcution scenarios during arti cail
lift activities (Sedarat et al. 2014, Silva et al. 2015,
AlHarooni et al. 2015). The required data such as pro-
duction rate data, average reservoir pressure, bottom
hole owing pressure, and well pro le data were used
as input data. The vertical multiphase ow correlation
and uid properties were utilized to determine produ-
ction rate as a function of gas injection rates. Injected
gas rate and production tubing size are the only main
parameters that affect well performance, however, since
production tubing is already xed in the reservoir, thus
injection gas rate can be controlled to optimize the well
performance.
The methodology of perform the simulation study
was taken by the method presented by Bahadori et al.
(2001). The following steps were followed to perform the
simulation and optimization study of gas lift system. In
the rst step of this study, appropriate uid properties
correlations were selected. Then, pressure travers (P
t
)
inside the tubing string was calculated. Then, different
values of GLR and production rates were assumed and
gas injection pressure (P
g
) in the casing was calculated.
The values of P
t
and P
g
were compared and if P
t
=P
g
-ΔP-
valve
, the depth of injection was determined. The well head