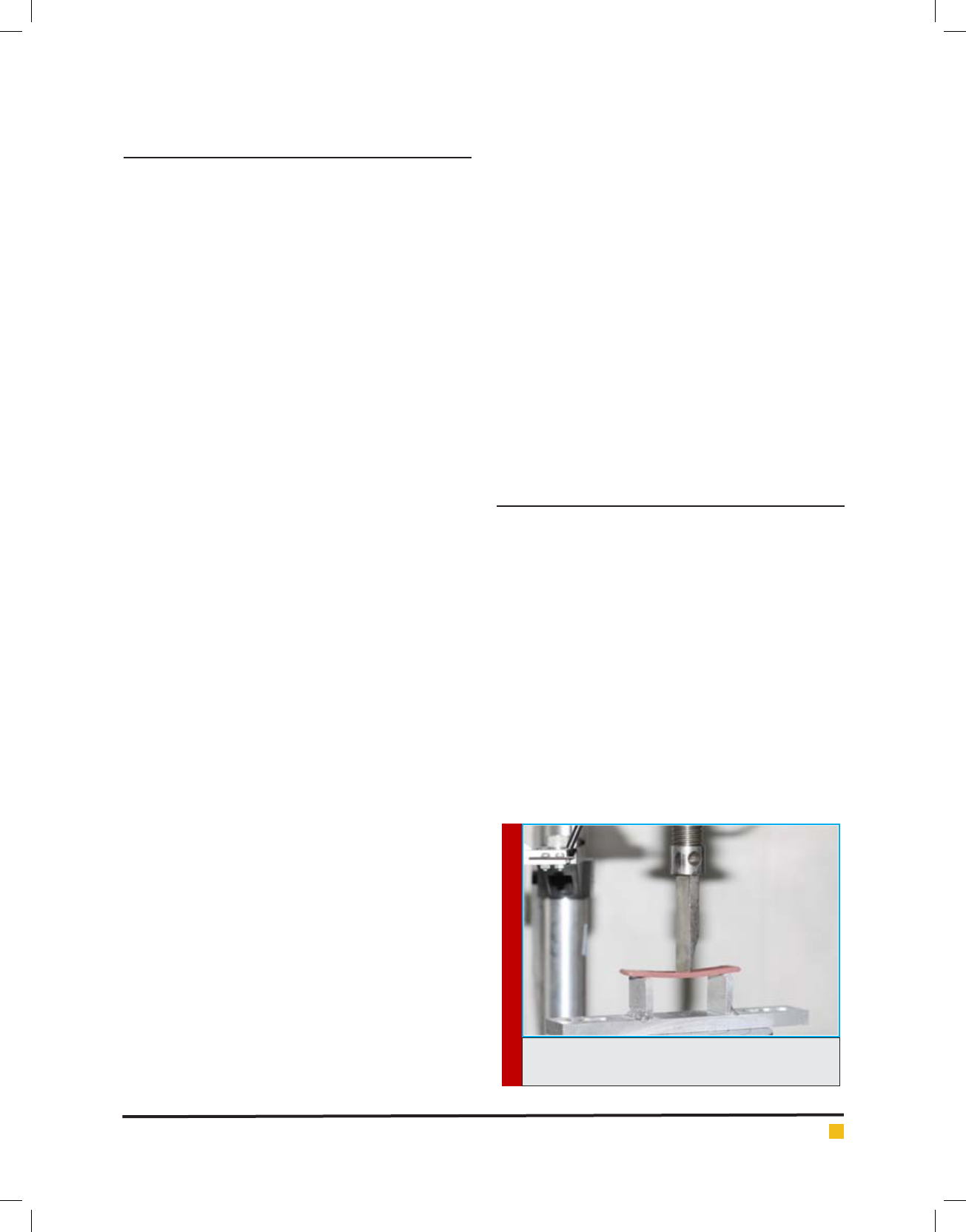
Hamid, Saba and Marzieh
INTRODUCTION
Poly methyl methacrylate (PMMA) material as denture
base material which is more preferred material than
the other denture base materials (Rickman et al. 2012).
PMMA is routinely produced by suspension or emulsion
polymerization. PMMA is formed by addition polymeri-
zation of multiple methyl methacrylate monomers in the
presence of an initiator, typically benzyl peroxide (Alla
et al. 2011). The PMMA is usually used for the construc-
tion of removable partial or complete dentures (Raj and
D’Souza 2011). In heat-cured materials, the polymeriza-
tion process is initiated by the release of free radicals
from benzyl peroxide on supply of heat energy (Ginju-
palli et al. 2012). These free radicals react with the mon-
omer molecules and continue till the monomer is avail-
able (Bhatia et al. 2013). These materials are supplied in
the form of powder while liquid form of them contains
nely divided pre-polymerized PMMA beads and liquid
contains methyl methacrylate (Gosavi et al. 2013).
The transverse or exural strength test, one of
mechanical strength tests, is especially useful in com-
paring denture base materials in which a stress of this
applied to the denture during mastication. The trans-
verse or exural strength is a combination of compres-
sive strength, tensile, and shear strength, all of which
directly re ect the stiffness and resistance of a material
to fracture (Ersu et al. 2009). The transverse strength
of acrylic resins depends on numerous factors including
polymer molecular weight and bead size, residual mono-
mer level, plasticizer composition, cross–linking agent,
internal porosity of the polymer matrix, denture base
thickness, patient factory and action of chemical agents
(Gurbuz et al. 2010). Physical properties of the denture
base are important for longevity of dental prosthesis
(Tugut et al. 2012). Transverse strength of acrylic resins
is reliable method to estimated resin behavior under dif-
ferent experimental conditions (Tugut et al. 2012).
Essential requirement for denture base polymers are
adequate mechanical properties, suf cient aesthetics,
hygiene, easy handling of resins and minimal release of
residual compounds such as residual monomer (Raj and
D’Souza, 2011). To solve this perplexing problem, it is
reported to altering the PMMA surface before applying a
resilient material (Tugut et al. 2012). In this regard, sand
blasting procedure has been introduced which involves
spraying a stream of aluminum oxide particles against
the material surface intended for bonding under high
pressure (Chung et al. 2008). Limit information exist
on con icting on use of sandblasting to increase bond
strength of acrylic resin denture base and soft lining
material (Ersu et al. 2009).
To decrease the denture fracture incidence, various
aspects can be considered such as optimizing chemical
structure and processing techniques; improving adhe-
sion; altering composition either chemically (using
high impact polymer) and making physical alterations
(incorporate materials such as bers, metal into PMMA)
(Gharechahi et al. 2014; Nejatian et al. 2015).
Because of the risk of fracture should a patient drop
their denture, high impact strength is a desirable prop-
erty. Given the function of a denture base in a removable
prosthesis, high exural strength, exural modulus, and
a large yield point distance would help resist torsional
forces in function leading to a longer clinical service life
for the prosthesis (Meng et al. 2005). So, in the current
study we tried to comparison of transverse strength of
three different types including heat cure acrylic with-
out any reinforcement, heat cure acrylic reinforced with
1mm sand blast metal wire and heat cure acrylic rein-
forced with 1mm sandblast metal wire that impregnated
with 4meta bonding agent (U Bar).
MATERIAL AND METHODS
In this study 30 heat cure acrylic (Meliodent, HERAEUS
KULZER, Germany) in dimension s (70mm 15mm
3mm) were used. In rst group heat cure acrylic samples
without any reinforcement, second group samples were
reinforced with 1mm sand blast metal wire and third
group, heat cure acrylic was reinforced with 1mm sand-
blast metal wire that stained impregnated with 4meta
(4-methacryloxyethyl trimellitate anhydride) bonding
agent UBAR Metal Bonding Cold Cure – Bonding Liner
(Pro Tech, USA). For group 1, the acrylic where mixed as
24.3 g powder in 10CC liquid, proceed in the generator
at 75°C for 8 h, then samples de asked and polished.
In the second group the 1mm sand blast metal wire
(DENTAURUM GmbH & Co. KG, Germany) was applied
using aluminum oxide using Topstar (Bego, Germany).
To insert wire into the acrylic, after press and remove
FIGURE 1. The transverse strength of the samples
using universal testing machine
BIOSCIENCE BIOTECHNOLOGY RESEARCH COMMUNICATIONS COMPARISON OF TRANSVERSE STRENGTH OF THREE DIFFERENT TYPES OF HEAT CURED RESIN ACRYLICS 249